
Principles of Cleanroom Design and Construction Across Various Industries
Introduction
The cleanroom is a modern concept with a history of over 100 years, initially developed for bacterial control in hospital operating rooms. According to ISO 14644-1 and Federal Standard 209E, a cleanroom is a controlled environment where airborne particle concentrations are regulated, and parameters such as temperature, humidity, and pressure are adjusted to specific requirements. Cleanrooms have become essential in modern industrial production, with wide applications in various industries:
Electronics: Manufacturing of magnetic tapes, flat panels, computers, etc.
Semiconductors: Production of memory circuits, computer controls, etc.
Micromechanics: Production optical disc drives, etc.
Optics: Manufacturing lenses, laser equipment, photographic films, etc.
Pharmaceuticals: Drug production.
Biotechnology and Hospitals: Producing antibiotics, genetic engineering, and patient isolation.
Principles of Cleanroom Design
Designing a cleanroom requires adherence to key principles for minimizing contamination and compliance with international standards. These include:
- General engineering standards.
- Standards for controlling biological and pharmaceutical contamination.
- Standards for controlling chemical contamination.
The evolution of standards, particularly in industrialized countries, highlights the growing importance of cleanrooms. Approximately 30 new or revised standards are introduced annually. To achieve optimal design, designers must identify the most critical contaminants.
The primary contamination concern in cleanrooms is airborne particles, though other pollutants that could harm products, processes, or operators must also be considered. For example, in pharmaceutical or biological cleanrooms, microorganisms carried by particles are a key concern. Designers must evaluate which contaminants are most relevant to the specific cleanroom requirements.
Designing, constructing, and maintaining a cleanroom requires understanding the relationship between room design, surface materials, operators, and the cleanroom class. The needed class and standards depend on the tasks performed within the cleanroom; higher standards are necessary for more contamination-sensitive products.
Factors to consider in cleanroom design include airflow patterns, air velocity, HVAC, temperature, humidity, pressure, microbial contamination, noise, vibration, electrostatic interference, and cleanroom lighting.
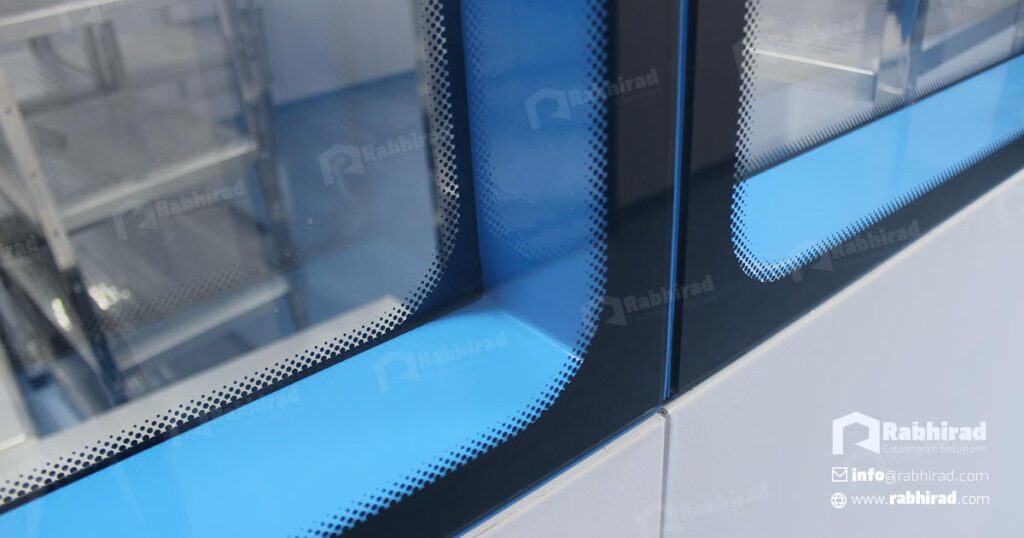
Site Selection for Cleanroom Construction
The site selection process for cleanroom construction involves considerations such as:
- The load-bearing capacity of the ground.
- Toxicity of groundwater and soil.
- Ambient air quality and pollutants like particulates and microbial contaminants.
- Quality of the site’s water supply.
- Environmental issues related to air emissions and waste disposal.
- Levels of vibration and environmental noise at the site.
- Environmental electromagnetic fields.
- Security and access control.
- Local zoning regulations.
Cleanroom Construction Materials
Selecting appropriate construction materials is critical to maintaining cleanroom integrity. Generally, materials should be seamless, non-porous, non-shedding, easily cleanable, and durable to minimize particle generation. Commonly used materials include:
- Non-flammable composite panels with aluminum frames and unplasticized PVC (uPVC) coatings on galvanized steel with aluminum honeycomb cores.
- Glass-reinforced plastic (GRP) wall panels.
- Epoxy-based systems.
- Stainless steel, aluminum, painted steel, and fiberglass.
Safety and Design Considerations
Cleanroom design should prioritize contamination control. Sources of contamination include airborne particles, chemical gases, and biological agents. Computational fluid dynamics (CFD) modeling and airflow analysis can help identify and mitigate contamination pathways. Differential pressures between spaces and airlock designs are essential for preventing contamination transfer.
Door mechanisms must account for room pressure, with doors typically sealed by room pressure unless they serve as emergency exits. Sealants are essential to maintain pressure and minimize air leaks.
Interior surfaces should be smooth and non-porous to facilitate cleaning. Emergency exits and security systems must prevent unauthorized access.
Construction processes inherently generate contamination; thus, traditional construction methods must be adapted to meet cleanroom needs. Continuous cleaning during construction is essential to prevent particle buildup. Positive pressure should be maintained in the cleanroom to prevent dust intrusion.
All equipment and materials entering the cleanroom should be cleaned and sealed beforehand. Workers must follow cleanroom-specific protocols, including wearing safety gear like gloves, special footwear, and protective caps.
RabHirad
Designing and constructing a cleanroom requires technical expertise, adherence to up-to-date standards, and the use of suitable materials and equipment. By following these principles, a safe, clean, and efficient environment can be created for sensitive industries.
RabHirad specializes in cleanroom design and construction, leveraging years of experience and engineering expertise to deliver projects that meet the highest standards and provide secure, efficient solutions for critical industries.
Source:
WEI SUN. ASHRAE DESIGN GUIDE FOR CLEANROOMS: Fundamentals, Systems, and Performance. ASHRAE.
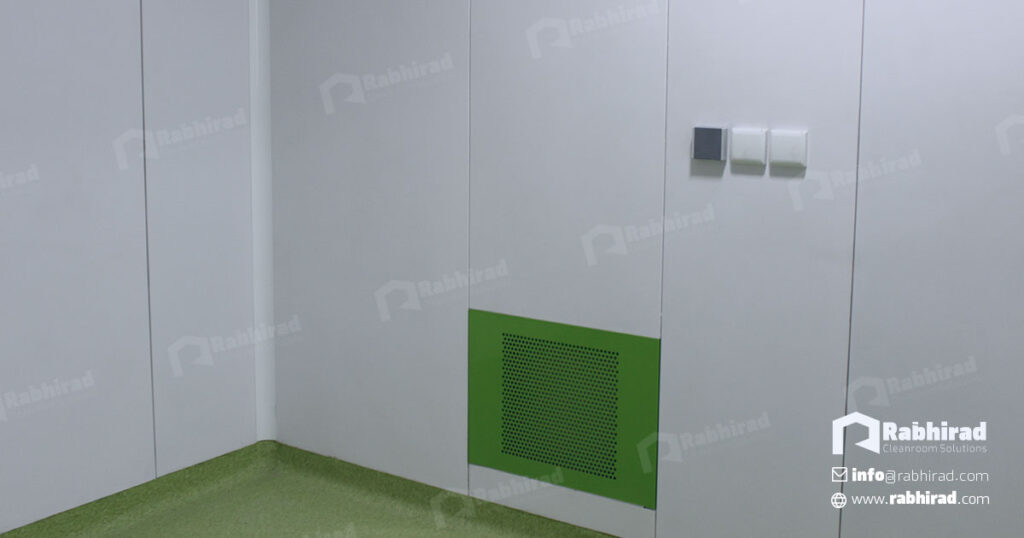